SealBoss in Panama and Colombia
SealBoss in Panama & Colombia
SealBoss International Product Training
SealBoss Technical Reps train contractors and educate engineers worldwide.
We regularly provide classroom style seminars and a hands-on experience. We offer jobsite training for contractors and work crews.
If you like training or assistance on the job, please contact your SealBoss Technical Rep at any time for further information. Or please call the main office at +1 714-662-4445 with any questions you may have.
With offerings spanning the waterproofing, floor repair, and structural repair scopes,
SealBoss is your source for proven concrete repair materials.
Injection Tube Installation in Panama
Panama City, Panama
SealBoss 1510 Water Stop Foam and SealBoss Injection Tube System Type 2 have been specified for use in the early construction stages of a high end shopping center in Panama City, Panama.
The water table is 7 meters below grade. A large topping slab will be poured atop a footing. The resulting cold joint between the slab and the existing shotcrete wall needs to be sealed to prevent water intrusion. The SealBoss Injection Tube System is placed at the midpoint of the topping slab’s 1 foot (30 cm) thickness.
After full cure of the poured concrete, subsequent injection of SealBoss 1510 Water Stop Foam trough the SealBoss Injection Tube System tube system will create tight seal between the outside edge of the topping slab and the existing shotcrete wall. Each tube run has a length of approximately 20′ (6 m).
Meeting with Customers in Medellin, Colombia
Medellin, Colombia
A SealBoss international technical rep is traveling to Colombia to train customers in the Medellin area. The SealBoss injection systems and floor repair product line, including the JointMaster pumps, are available throughout the South American continent.
Please contact us directly for product and sales rep information in Colombia.
Contact Your SealBoss ® Technician
SealBoss SLP Polymer Pump Systems
Polymer Pump Systems
Signature Line Air-Powered Polymer Pumps
Design Cues
• Industrial Grade Lightweight Design
• Robust, Modern Steel Frames
• Advanced Piston Pump Systems
• Newly Designed Applicators
Range of Materials
• Polyurethane resin
• Polyurethane foam grout
• Epoxy Resin
• Aqueous solution
Advantages
• Extremely lightweight designs
• Robust, heavy duty components
• Large material passages for use of products with higher viscosities
• Piston seals do not require tensioning
• Easy maintenance and repair
• Pneumatic design
Four SLP Signature Pumps
The SealBoss SLP Pump Signature Line of single and multiple component, pneumatic reciprocating piston injection machines are newly developed, professional and purpose built heavy duty air-powered injection pumps. They complement our existing comprehensive line of pneumatic, electric and hand operated pumps.
In the following we point out some advantages of air-powered equipment. Our pneumatic pumps are easily maintained, highly reliable and very easy to use. Air flow is effortlessly controlled and our pumps perform very well at low and high rates of product flow. Our pumps feature relatively large internal clearances in the major fluid passages (i.e. large intake and discharge openings), that allow liquids of higher viscosities to pass.
Air-powered pumps have been highly developed to provide long-term reliability and durability even under difficult injection conditions. With the air-powered design there is inherently less mechanical load and wear on key components than with other designs. Long term durability is achieved by the relatively low-speed, high clearance nature of the moving parts. Air-powered pumps have a unique advantage in their ability to throttle back flow to meet changing site needs. Stop/start cycle limitations do not apply to these pumps, so no adjustments need be made when dispensing rates decrease; the air-powered pump will function as intended, at a reduced refill/discharge cycle rate. If pump output rate reduction is desired, the applied air pressure can be easily adjusted downward with the provided regulator.
With air-powered pumping systems, airlines are run to the pump instead of electricity, which provides immediate benefits in simplicity and safety. Pumps are delivered as a complete system, with all the necessary tubing, connectors and applicators.
Service is easy due to mechanical simplicity, lightweight and ease of handling. If pump operation is stopped due to clogging or back-pressure, typically no structural damage to the equipment occurs.
Conclusion
Air-powered pumps provide many advantages in injection applications equipment. A proven approach is to inform the pump supplier of the full conditions of the application and obtain a recommendation for the suitable equipment. It is important to research the quality, performance and suitability before selecting either an electric or air-powered pump.
Contact Your SealBoss ® Technician
SealBoss at World Of Concrete 2019
World of Concrete 2019
Meet with Your SealBoss Rep at WOC 2019
SealBoss will be at World of Concrete 2019! See us at Booth # S13239
Learn more about our crack injection systems, hydro active foam grouts, gels, PU resins
Get detailed info on SealBoss epoxy injection technology, epoxy resins & paste
Experience the SealBoss QuickFix polyurea joint filler and floor spall repair products
Get in-depth instruction on using and cleaning our Epoxy Pumps, Injection Pumps, and see the outstanding SealBoss JointMaster Joint Filler Pump
Explore our extensive packer selection and Inject Tube Systems
Also: Hot Shot Cartridges, swellable joint sealants SwellCaulk, in tubes and cartridges, and SwellTape
Contact Your SealBoss ® Technician
SealBoss at ICRI Fall Convention
ICRI Fall Convention
Technical Sessions, Networking and Social Events
ICRI FALL CONVENTION
“Resiliency: Above and Beyond Concrete Restoration”
SealBoss proudly supports the ICRI at their Fall Convention in Omaha.
Thanks to the ICRI and everyone who came by to visit the SealBoss table.
Leadership, fellowship and learning are the foundation of our business.
Contact Your SealBoss ® Technician
SealBoss JointMaster Joint Fill System
Jointmaster Joint Fill System Training
Hands-On Floor Repair Training with the JointMaster Joint Fill System
Our technicians train a Los Angeles concrete polishing contractor in the use of the SealBoss QuickFix Floor Repair System
We mated our joint filler product with our advanced dispensing machine to create a powerful system that works seamlessly and effectively. In less than 30 minutes a ‘new to the system contractor crew’ can be up and running with a smile on their face.
The highly practical and sturdy JointMaster Pro2 joint filler pump and the SealBoss 6500 QuickFix polyurea polymer joint filler are your proven tools for professional and long lasting joint repairs. We provide on-the-job training to get you going and fill you in on tips and tricks of the trade.
JointMaster & QuickFix Polyurea – A Professional and Affordable System Solution
Built from heavy duty components our JointMaster pump design has evolved and has been continuously improved for over more than a decade. Our systems are affordable and supported by us, even if you purchase through your local distributor.
Cartridge System available for smaller jobs
For smaller jobs we also provide our joint fill and spall repair products in a cartridge system. SealBoss 6500 and SealBoss 6060 Cartridges can be dispensed with our hand operated, pneumatic and battery operated guns.
Contact Your SealBoss ® Technician
SealBoss at NJ Golf Outing
MBSI Golf Outing New Jersey / NYC
SealBoss at SWR Institute Fall Meeting
SWR Institute Fall Meeting
SealBoss in Argentina & Uruguay
SealBoss - Argentina & Uruguay
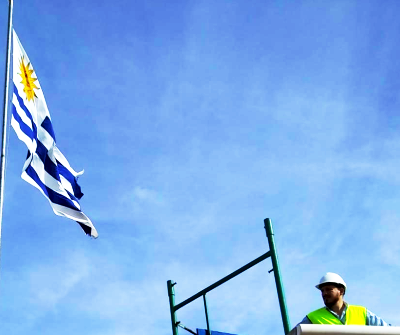
SealBoss Technical Representative visits customers and projects in Argentina and Uruguay
We thank our business partners for the generous hospitality and the exciting opportunities to utilize our products and expertise.
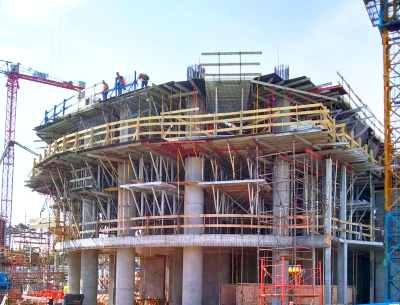
SealBoss Guideline Leak Seal Injection
Guideline - Leak Sealing Injection
This jobsite picture depicts one of the more challenging overhead leak sealing injection applications in a confined space with limited resources, very active water leaks and standing water in the structure. The contractor is using a button-head packer set-up for a secure and leak free connection of the hose to the injection packer. On the ceiling of the structure you can see previous injection points and cured foam that formed around the injected cracks while expanding and creating a compression seal. The contractor is covered in impervious protective clothing to protect himself from water and liquid product during the injection process. It is during jobs like this, when you appreciate a complete injection system that is proven, reliable and durable.
This is our compact guideline to waterproofing and leak sealing injection. From choosing product and equipment to job prep and the injection procedure itself, we cover many important product features and provide valuable information to assist you in making your application a successful one.