Field Service / On-the-Job Training / Jobsite Assistance | Wherever / Whenever You Need It
We’re There
When You Need Support
Quality Products & Service
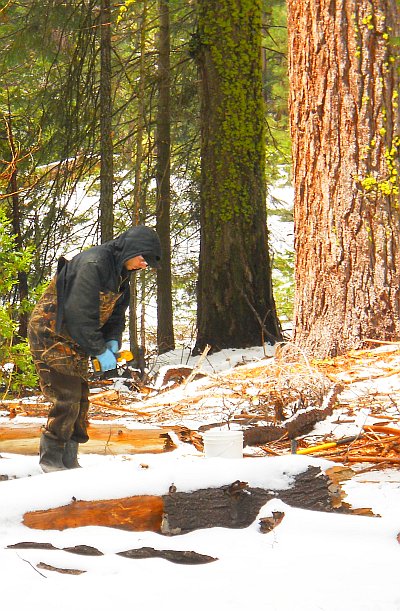
Your construction or repair job cannot be put on hold. You may need support or training on very short notice, sometimes on weekends, at night or during holidays. We will always do our best to be there for you when you need us.
For over three decades, our experienced team of technical representatives has been on-site for you providing field service, consulting and quality training in the U.S. and worldwide, including Canada and Mexico, Asia, Australia, New Zealand, Central & South America and Africa.
Our field services and trainings cover the complete line of products – Leak sealing injection, structural epoxy injection, cold joint repair systems, floor repair systems and joint fill systems, as well as geotechnical soil stabilization, void filling and lifting. We provide you with training on our many pumps and dispensing systems.
We are here to help you when you need us – our track record speaks for itself.
Rain or Shine – Snow or Heat
SealBoss Provides
Reliable Field Service &
Quality On-The-Job Training
“While providing on-site support and training, we create a positive learning environment focusing on building applicator confidence allowing for successful repairs to be continued after the training. From training new companies and their employees, SealBoss has continued to provide support to our clients for over 32 years.
On-site training consists of an overview of products, the pump and it’s features. This is followed by hands on training with actual dispensing of material on the job site until the applicator has gotten confident with the application techniques and nuances of the material used. Finally we focus on the correct cleaning procedure of the equipment.
We won’t leave a jobsite till I know everyone is comfortable with the systems and can reteach the next person in line.
With a knowledgeable technical support team, we are here to help with any questions you may have”
SealBoss Technical Support Team