Epoxy Injection Preparation Tips

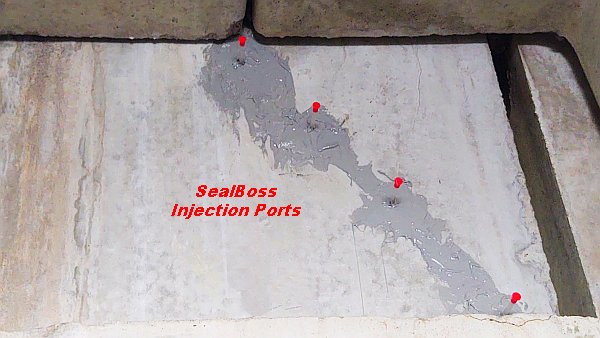
Introduction:
Epoxy injection is a highly effective, polymer delivery method through a pumping system for repairing cracks in concrete structures. This process involves sealing all accessible sides of a crack and bonding them with a high and strength, low-viscosity epoxy resin by pressure injection.
Proper preparation is crucial for successful epoxy injection. It begins with cleaning the crack thoroughly, surface sealing the crack, and installing surface mount Tri-Base ports along the crack at specific intervals with a fast setting, non-sag epoxy paste. Following these preparation steps ensures the epoxy resin can penetrate and bond the cracked concrete effectively, restoring its structural integrity in the process.
Epoxy Injection Preparation Tips – Installing Surface Mount Tri-Base Ports
Epoxy Injection is a typically a low pressure to medium pressure crack filling solution where all sides of the crack are sealed and structurally glued together with a high strength low viscosity Epoxy Resin.
To prep for injection, the crack must be cleaned with a wire brush and all dust removed. Any surface contaminants, such as oils or paints, must be removed for the epoxy paste-over to bond properly. If available, use clean compressed air to remove any dust and debris. For best results perform epoxy injection preparation when the crack and surface are dry. Any water seeping from the crack should be stopped prior to epoxy injection. For sealing water bearing cracks click here.
Once the surface is cleaned, the Surface Mount Epoxy Injection Ports are installed directly over the crack 6” – 8” (15-20 cm) apart. The finer the crack, the narrower the spacing should be.
Shown in this example are standard surface mounted Tri-Base ports, however corner ports and ½” drill in ports are available for specific applications.
Tri-Base Ports are mounted by placing epoxy on each of the three tabs on the base of the port. Once ports are placed, the non-sag paste is applied to both sides of the wall, sealing the crack.
When applying paste, the mixed material should be applied generously at roughly 1/8” (3-4 mm) thickness, and mounded up around each port to approximately 1/4″ (6-7 mm) thick or more using a putty knife or other suitable tool. The paste-over should be a minimum of 1 inch (3 cm) wide along the crack. If the paste is not applied thick enough it may crack and epoxy will escape during injection, preventing proper penetration and epoxy flow within the crack itself. Note: The length of time needed for the epoxy paste to fully cure varies with ambient and substrate temperature.
“ Once ports are placed, the non-sag paste is applied at roughly 1/8” thickness and mounded up around each port. If the paste is not applied thick enough it may crack open and epoxy will escape during injection. “
After the surface paste has hardened, structural strength epoxy resin can be injected starting at the lowest port on the crack, for horizontal or lateral cracks start on one side and work your way over.
Because the crack has been sealed on both sides, the next port in line will need to have the cap removed to allow the displaced air to escape. Once the Epoxy resin can be seen escaping from that next port injection stops, the applicator is disconnected from the injected port and the port is capped.
The applicator is then connected to the next port and the process is repeated. Once the crack has been fully injected and the Epoxy resin has cured, ports and paste can be ground off for aesthetics.
Epoxy does not Flow as Expected – Troubleshooter
- Injected crack is not continuous or the area being injected is saturated
- Crack is blocked by debris or cured epoxy paste
- Surface mount port does not align with the crack
- Epoxy has cured in injection nozzle, port or crack
- Epoxy resin viscosity too high
Epoxy injection is an efficient and economical method of repairing cracks in structural concrete walls, slabs, columns and piers. If applied in compliance with all recommendations and specifications, high strength epoxy is capable of restoring concrete structures to their strength prior to crack development.
If at any time during your epoxy injection preparation and any other repairs you encounter issues that can’t be resolved, please call us here at SealBoss for support – 714-662-4445. Your technical representative will gladly be of assistance.
At SealBoss, we offer full system solutions for Structural Epoxy Injection Repairs including Electric and Pneumatic Pumps, various Ports, Epoxy Resins, Paste and Cartridge System.